-Pamela Caudillo, Content & Communication
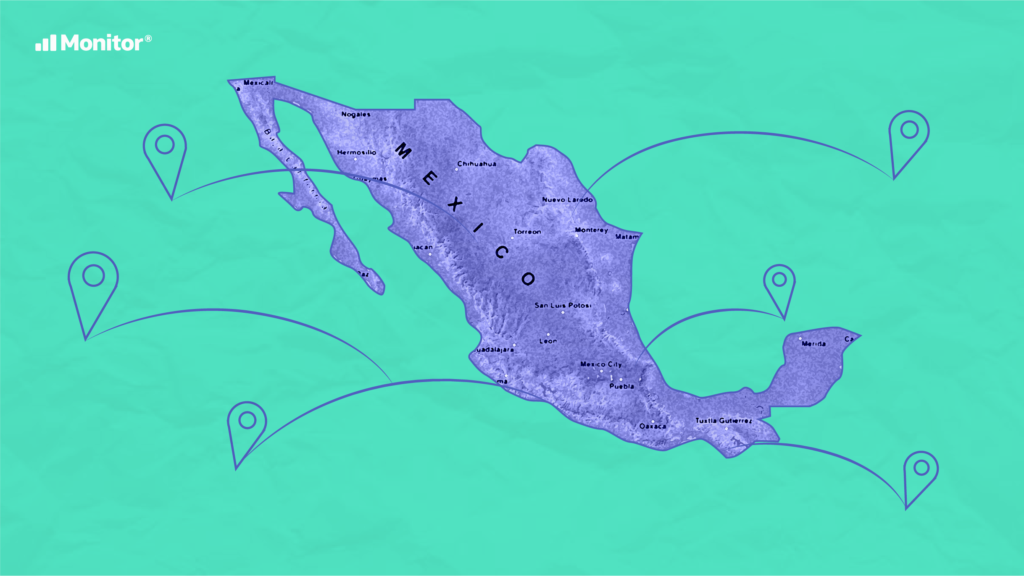
Supongamos que hemos tenido la siguiente pesadilla manufacturera:
Nos encontramos justo en medio de una crisis mundial derivada de la todavía existente pandemia de la Covid-19, y una guerra entre Rusia y Ucrania que está poniendo a las cadenas de abastecimiento de cabeza. Entonces volteamos hacía la industria nacional, donde nos vemos afectados por una inflación que ha llegado a un 8.62%, lo cual nos preocupa porque esto lleva a que haya menos consumidores de electrodomésticos. automóviles, teléfonos celulares, equipos de cómputo, etc.
Parece un escenario apocalíptico para la industria manufacturera, ¿no?
La industria manufacturera tiene problemas por donde se vea, tanto para producir, dada la escasez de materia prima a causa del rompimiento en las cadenas de suministro a nivel internacional (tal es el caso de la planta de GM, Silao, y su falta de semiconductores), así como para la venta del producto final dada la situación económica mundial, lo cual afecta a las ganancias de los distribuidores, OEMs, Tier 1, etc. Entonces, la pregunta obligada es, ¿si tenemos problemas para producir, y también para vender, todo está perdido para la industria manufacturera mexicana?
La respuesta más allá de un simple sí o no, se trata de qué tan estratégicos seamos, es decir que tanto le saquemos provecho a una maniobra conocida como “Nearshoring”.
¿Qué es el Nearshoring?
Antes del brote de Coronavirus, las grandes empresas acostumbraban transferir sus procesos de manufactura o negocio a terceras partes ubicados en lugares alejados de la sede de las compañías (comúnmente al continente asiático) con el fin de reducir costos de producción, lo que se conocía como “Offshoring”. Al entrar en estado de emergencia sanitaria, y verse severamente afectadas las cadenas de suministro se buscó optimizar estos procesos, con tal de garantizar el abastecimiento. Es entonces que las grandes corporaciones optaron por subirse al tren del Nearshoring, que consiste en llevar sus servicios a empresas de países cercanos a las sedes de estos gigantes comerciales.
Con este cambio en el modelo de producción se buscó eficientizar las cadenas de suministro para amortiguar el golpe de escasez, originado por la pandemia. Al iniciar el año, y ver que la tensión militar en Ucrania derivó en una guerra y tensión mundial sin igual, se volvió más importante para las empresas asegurar su producción.
Mediante el traslado de su producción a países cercanos, tal es el caso de la compañía estadounidense Ford, que ha instalado plantas de producción en Sonora, Coahuila y Chihuahua, las empresas aumentan su capacidad de respuesta a las necesidades de sus clientes, teniendo tiempos de entrega más cortos y más flexibilidad ante futuras crisis.
¿Cómo podemos sacarle ventaja al Nearshoring?
México se encuentra en una posición geográfica privilegiada dada su vecindad con Estados Unidos, que es el mercado más grande a nivel internacional. En específico, al firmar el tratado de libre comercio con Canadá y Estados Unidos, donde se requiere por lo menos un 75% de VCR (Valor de Contenido Regional) en la producción de automóviles y autopartes, México se ha convertido en un destino atractivo para empresas extranjeras que busquen llegar al mercado estadounidense con preferencia arancelaria. Tal es el caso de la china JAC y su instalación en Hidalgo, o las japonesas Honda, Mazda y Toyota en Guanajuato.
Algunas cualidades que hacen a la industria manufacturera nacional más competitiva son:
- Costos laborales bajos
De acuerdo con Datos macro, de expansión, en 2020 el salario semanal promedio en México fue de $198.70 dólares, contra $318.8 dólares de China, lo que promueve el traslado de la mano de obra a nuestro país (aún estando dentro del nuevo acuerdo salarial del TLCAN).
- Un coste logístico menor
México cuenta con 117 puertos marítimos, 64 aeropuertos internacionales, 27 mil km de vías férreas y 172 mil km de carreteras. Lo cual promueve una fluidez en el transporte y exportación de materias primas y/o productos terminados.
- Cadenas de abastecimiento
El transporte de los bienes de suministro entre Estados Unidos y México toma en promedio 3-4 días (por tierra), contra las semanas de espera que tarda un embarque transpacífico. Así se reduce el riesgo en la cadena además de un ahorro monumental en los costes de transporte y almacenamiento.
El lado B del paraíso
Aunque México es el semillero perfecto para que empresas asiáticas y europeas traigan su producción y beneficien así a la industria y economía nacional, existe un margen reducido ante el cual estamos en desnivel. Nos encontramos ante una evidente desventaja tecnológica, y con una todavía incipiente integración a la industria 4.0. Pero ¿Cuál es la importancia de la IA y el IIOT en este escenario?
Empresas Tier 1 como ZF, principal proveedor de compañías como BMW, y Fiat Chrysler Automobiles, están apostando por digitalización completa de sus procesos y cadenas de suministro. Con su plataforma SupplyOn, pretende que todos sus proveedores empaten sus procesos logísticos y de calidad con la empresa alemana. De este modo busca asegurar la fluidez y abastecimiento de sus cadenas de suministro, la calidad de sus componentes, garantizar la eficiencia de sus procesos logísticos, así como asegurar sus sistemas de producción ante posibles perturbaciones.
Y es que no basta solo estar cerca del objetivo para que la industria mexicana pueda explotar el Nearshoring, si se quiere impulsar la producción nacional para atraer más inversores, es necesario garantizar el proceso de exportación desde el abastecimiento de materias primas hasta la entrega del producto.
El cóctel perfecto…Transparencia, Competitividad, y Eficiencia
Para que la industria nacional pueda seguir a flote pese a las diversas crisis y amenazas es necesario que proveedores como ZF sean capaces de confiar y apostar por la industria mexicana. Tarea que podemos lograr al incorporar soluciones 4.0 que brinden:
- Transparencia
Ser capaz de detallar los tiempos exactos de producción, tener el recuento de desperdicios, y mostrar la capacidad de producción real a través de una radiografía del sistema de producción, como lo es un gemelo digital.
- Competitividad
Ser conscientes de los alcances y aprovechar al máximo los equipos y maquinaria a través del OEE, hace a la organización competitiva frente a otras empresas al explotar su capacidad plena.
- Eficiencia
Conocer el proceso de producción permite realizar los ajustes necesarios para eficientar recursos (financieros, humanos, materiales), puesto que se ahorra tiempo, se aprovecha la mano de obra, y se conocen los procesos y variables críticas que pueden suponer un ahorro significativo, todo lo cual puede llevar a ofertar precios competitivos a los clientes.
La manufactura global se ha redefinido a pasos agigantados, y es necesario que la industria nacional le siga detrás, de lo contrario el escenario de una pesadilla apocalíptica se convertirá en una cruel realidad.
En Monitor App ® queremos que duermas tranquilo, y por eso te ofrecemos nuestra plataforma sencilla e intuitiva que llevará tus sueños hacía la realidad el paraíso de la manufactura. Adentrate al mundo de la industria 4.0 poniéndote en contacto con amaranta@monitorapp.io , o dando click aquí: