Pamela Caudillo, Content & Communication

En un mundo ideal, tener el superpoder de la predictibilidad nos ayudaría en una que otra situación, saber que sucederá a futuro y cómo anticiparse a ello sin correr riesgos sería una especie de solución mágica a los problemas cotidianos. En el mundo de la manufactura el arte de predecir se convierte en una cualidad aún más apreciada, la razón, ¿Quién no desearía tener una producción perfecta, cero defectos, sin contratiempos y con total aprovechamiento de recursos?
Por más increíble que parezca, existe una herramienta tecnológica que nos da una vista hacia el futuro cómo si de una bola de cristal se tratara, los Gemelos Digitales unen nuestro mundo físico con el digital para darnos una aproximación casi exacta de lo que sucederá, permitiéndonos ir un paso delante de los riesgos.
¿Qué es un Gemelo Digital?
Al ser un término poco empleado en nuestro lenguaje cotidiano, pensamos que un Gemelo Digital es exclusivo del mundo de hackers o científicos, pero, se encuentra presente en nuestra vida cotidiana y los usamos por ejemplo en nuestros Smart Watch, mediante el cual recibimos mensajes y llamadas como si se tratara de nuestro teléfono mismo, gracias a la conexión que mantiene con él. Al ser una copia del sistema nos permite realizar nuestras actividades sin tener forzosamente nuestro dispositivo a la mano.
Otro ejemplo un tanto más rudimentario sería el tablero de nuestro auto, que al recibir información mediante la instalación de sensores en el motor nos comunica el estado exacto de nuestro vehículo sin tener que abrirlo a cada instante para saber la cantidad de combustible que aún nos queda para realizar el viaje.
Es decir, los Gemelos digitales son una representación o réplica digital de un dispositivo o proceso físico, realizada a imagen y semejanza del original que mediante la incorporación de datos en tiempo real obtenidos a través de sensores reúnen información acerca del proceso y/o producto para que sea procesada con IA o sistemas en la nube, y así dar vida a una representación exacta que se comporta fielmente a la versión física.
El Gemelo Digital es creado para monitorear y analizar al objeto físico en cuestión en ambientes de simulación para dar una radiografía completa de su desempeño, en el caso de su aplicación a la industria manufacturera cumple la función primordial de visualizar escenarios de producción óptimos para detectar problemas antes de que puedan ocurrir.
Permitirá el mejoramiento general de los procesos productivos mediante el monitoreo total del sistema, dando lugar a la realización de previsiones a futuro, con posibilidades que van desde el realizar mantenimiento predictivo o planificar nuevas configuraciones de planta, sin alterar el funcionamiento real de la maquinaria.
La eficacia de los Gemelos Digitales se encuentra en la obtención de una retroalimentación inmediata y detallada del sistema que permite aplicar distintas alternativas de solución a problemas de producción en tiempo real, es decir sobre la marcha, optimizando el proceso en tiempo récord. Siendo así que los usuarios del Gemelo Digital somos capaces de comunicarnos con el sistema físico y lo entendemos a profundidad mediante la visualización, análisis y ensayo digital.
De esta forma los Gemelos Digitales funcionan como traductores de los procesos de producción al permitirnos conocer el estado y comportamiento en tiempo real de un sistema tecnológico en datos que son fácilmente interpretados por el lenguaje humano.
¿Cómo se implementa un Gemelo Digital en un proceso manufacturero?
En MonitorApp® mediante la visualización total de las condiciones de los procesos de producción se da lugar a la creación de Gemelos Digitales fieles a los procesos físicos sin la intervención intrusiva de la maquinaria, mediante la instalación plug & play de sensores (no invasiva), recopilan información del sistema físico, para después a través de tecnología nube (respaldada por la seguridad de AWS) reflejarlos en nuestro dashboard que el usuario leerá de manera sencilla e intuitiva, es decir, permite que el usuario final entienda a profundidad el sistema para lograr una comunicación que promueva la acción y facilite la toma de decisiones.
Con MonitorApp® eres capaz de conocer el estado exacto de tu producción mediante el monitoreo de 30 indicadores clave de producción y 60 variables de proceso. Además de incrementar el OEE de tu organización, el poder controlar las variables críticas que intervienen en tu proceso productivo permiten una planeación estratégica y detallada de la producción. Un Gemelo digital mejora la calidad de los procesos productivos mediante:
· Predicción de Mantenimientos Preventivos y Correctivos
· Disminución de las paradas de producción
· Optimización de Costos
· Eficiencia Energética
· Mejoramiento de la calidad del Producto o servicio
· Control de la producción para evitar errores
· Disminución de los tiempos de inactividad en el proceso
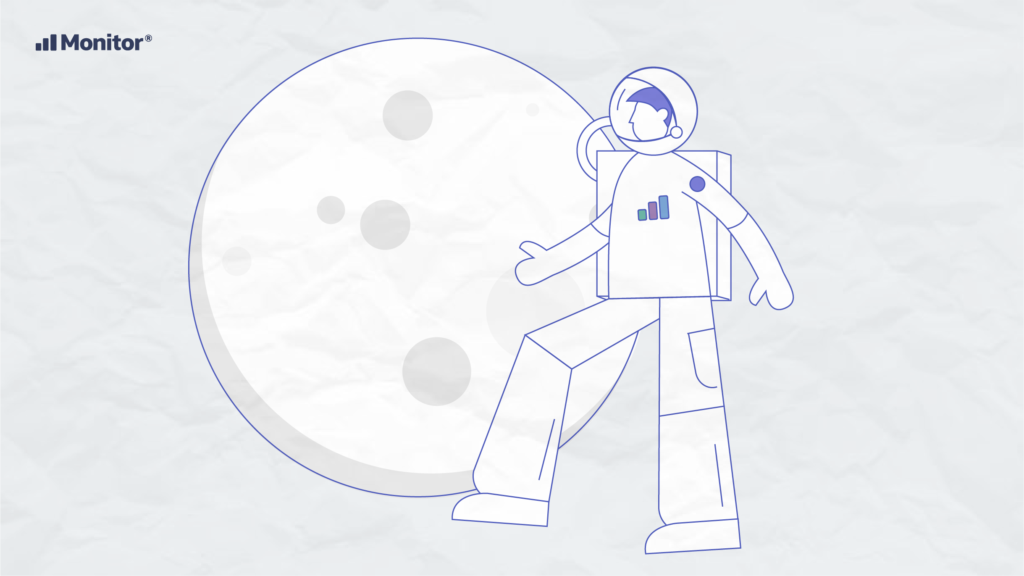
Gemelos Digitales, fundamento de la industria 4.0
Es posible adelantarse al futuro, por lo menos en cuanto a nuestro entendimiento de procesos, productos y servicios se refiere, gracias a los Gemelos Digitales se han logrado avances que van desde el aterrizaje a la luna, que marcó el inicio del nacimiento del término digital al crear una réplica del sistema que permitió el monitoreo y guía de la nave. Hasta nuestros días, en pleno auge de la industria 4.0, la creación de sistemas de producción eficientes que tienen como objetivo entregar al cliente el producto con la calidad óptima, mediante el mayor aprovechamiento de recursos y la disminución de riesgos operativos y financieros.
Atrévete y da un paso hacia el futuro de la industria, con Monitor App®. Contacta a amaranta@monitorapp.io
O bien, si tu también quieres comunicarte con tu fábrica mediante un gemelo digital da click al botón: